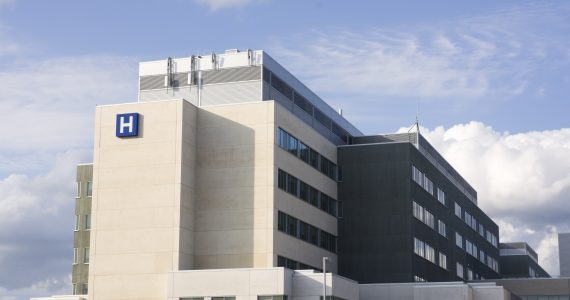
Maintenance in health care settings: an ounce of prevention
Health care facilities are critical buildings with a wide variety of technical installations. They require special attention to ensure patient safety. In this fast-changing sector, what are the maintenance issues, the areas requiring special attention, the expertise called for and the new expectations?
Stéphane Bretin, Business Unit Manager, VEF Facilities IDF Tertiaire, talks about his experience with maintenance in health care facilities.
1. What are the main maintenance issues in health care facilities?
Availability is one of the major issues, meaning uninterrupted operation of the installations, especially critical installations that are directly or indirectly contact with the patient. The other priority goals in this sector include:
- measurement and control of the energy impact of installation operation and maintenance
- health and safety in the patient environment,
- cost control throughout the building life cycle,
- and lastly innovation in an atypical sector that straddles the service sector (presence of end users, wide variety of services) and industry (processes, 24-hour service, technical installations, power used).
2. What medical systems require maintenance?
A wide variety of installations are subject to regulatory maintenance and/or inspection. Our business activity covers multi-technical installations far more than equipment in direct contact with patients. However, our bio-medical maintenance activity is substantial and highly regulated.
3. What are the areas requiring special attention on the part of the maintenance company?
The maintenance company must be highly familiar with the maintenance environment and with the risks to which it is exposed or to which it exposes its environment. Situations that can potentially result in a major crisis must be anticipated and immediately reported. Personnel without the necessary technical skills must be trained to do that and to work together to share information and assess the potential consequences. A work-around must be readily available at all times to cope with a crisis situation and ensure continuity of operations.
4. How does the operator build a maintenance policy?
Health care facilities have substantial and costly installations and systems. They must therefore provide for a large amount of preventive maintenance to identify and rapidly correct any slippage and prevent it from resulting in a major malfunction.
These are buildings with a long time scale that are subject to stringent regulations (water quality, air quality, electrical back-up, etc.). OEM parts, skilled personnel and rigorous management must be provided to ensure reliability of installations. The maintenance plan is drawn up and updated to take feedback on board in accordance with industrial continuous improvement programmes such as FMEA, 8D, 5S, etc.
5. What precautions should be taken when performing remote maintenance?
When properly conducted, remote maintenance can bring benefits. It is sometimes necessary, however, to carry out a sort of ex-post big-data review of the maintenance work and repairs carried out and compare them with the condition of the installation on the ground. Not everything can be picked up remotely. The sum of minor incidents can be more precisely audited in situ. Users, environments and local conditions are all factors that cannot be perceived by remote maintenance.
6. What practical advice would you give to maintenance companies?
My first recommendation would be to listen to the customer, occupants and end users to avoid getting off on the wrong track.
It is our responsibility to keep the installation clean and neat, and this type of primary maintenance will ensure immediate detection of any anomalies. This gives the maintenance company an incentive to take the approach a step further. We also need to ensure faultless traceability of maintenance work. Lastly, it is very useful to keep documentation/drawings up to date and to make information widely available.
7. What qualifications and expertise should a maintenance company have?
A wide variety of qualifications are required, depending on the building trade and scope covered and the level of expertise expected.
Similarly, the range of expertise required is as broad as the issues encountered on the ground and includes such things as PLC diagnostics, refrigeration circuit performance, unexpected shutdown of an alarm monitor, and so on.
8. What new services can we offer
In recent years we have broadened our traditional range of services to address the new issues encountered in the sector. One example is maintenance of small-scale health care facilities (mobile, small multi-service maintenance) to handle the full range of technical building and installation issues and offer one-stop-shop service.
These new services also include:
- Technical audits of IT facilities (patient data storage, service applications) followed by optimisation (surface area, reliability, etc.)
- Operational Building Information Modeling (BIM)
- Expanded end-user services
- Innovative IoT solutions to optimise management of consultation rooms
- Availability of an electronic air and water system record
- A hypervisor solution to concentrate and display data relating to operations, maintenance, comfort, energy, etc. within a building or across an entire facility.
The range of new services is very broad.
9. What are your customers’ selection criteria?
There are two main criteria: technical capability and cost – in other words, pricing to market within a rapidly changing sector.
Another article may interest you: Low voltage distribution board replacement in a hospital building: a high-voltage operation
Did you like the article ?