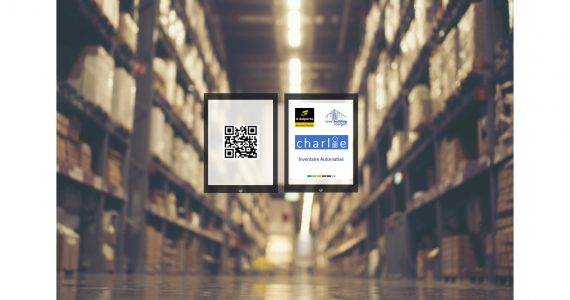
QR Codes and RFID chips: two automated inventory techniques
Managing worksite equipment (scaffolding, podium steps, hand tools, etc.) is a headache for our business units, which all have the same questions:
- What equipment is being used on a worksite?
- What equipment has been returned?
- What condition is the equipment in?
We take a look at two business units with different ways of answering these questions: SDEL Nantes and DELPORTE.
In Nantes, each piece of equipment has an attached bar code. These bar codes are read by a hand-held barcode scanner and the foreman or project manager can then scan a QR code on his or her badge to assign the equipment.
In Lille, SMART BUILDING Energies and DELPORTE are developing the “Charlie” application in partnership with the Noolitic company, which specialises in IoT.
The app works with RFID tags attached to each piece of equipment. Using a hand-held radio antenna, the foreman or project manager can scan the worksite and collect all the RFID tags corresponding to DELPORTE equipment; the only limitation is that the antenna must move at a distance of no more than 4 metres from the equipment.
The inventory is comprehensive and any missing item (for example, podium steps) can be identified, since each piece of equipment can be described as a set of several RFID tags.
If full-scale tests are conclusive, Charlie can be made available to other group business units.
Development is expected to be completed by the end of this year.
Did you like the article ?