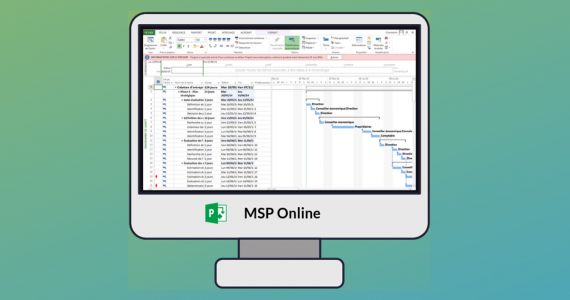
MSP Online: a collaborative project management tool
Najat SAOUF, who heads the Building Solutions Design Office in Morocco, took this initiative. A year after the tool was introduced, she shares her experience, explains the origins of the project and describes the first very promising results.
What is your background?
I joined Cegelec in 1999 as a design engineer in the Fluids activity. I remained in that position for nearly three years and then moved to a more operational job. From 2006 to 2009, I was selected to become Deputy Head of the Mamounia Hotel project in Marrakech.
In 2012, I was promoted to head of the design project on the Renault Tanger Med project, then head of the Design Office in the Fluids activity at Cegelec head office and finally head of the Design Office at the Building Solutions Division in 2016.
My experience in the field is an advantage. It enables me to identify the needs of operational personnel and anticipate their difficulties while retaining a comprehensive overview of the project.
Could you tell us more about your duties in the design office?
Our Design Office has expertise covering all building activities, including HVAC, smoke extraction, plumbing, fire protection, power supply, and ELV systems. Our office delves into the issues in all these areas, including structural design of equipment, costs to be budgeted and efficiency. It is also responsible for verifying the applicable standards and defining viable solutions.
In concrete terms, we provide expertise in two phases:
1. In the bidding phase, we take part in estimating projects. Our job is to optimise by submitting bids that set us apart from the competition.
2. During project execution, we prepare the deliverables, make recommendations based on calculations, and provide expert opinion on the quality of the projects.
The building solutions activity has doubled over recent years and now accounts for €50 million in revenue at Cegelec Maroc. This strong growth impacted the size of our Design Office, which now employs 40 people, including 10 engineers.
Why did you introduce a project management tool?
We had identified a recurring problem with the calculation of the work and cost indicators.
Every month, our engineers calculated the indicators manually, which took up about 20% of their time. More specifically, they had to enter the number of hours that each technician spent on each deliverable. We had a lot of trouble obtaining reliable information and we did not have an overview of the actual progress made on the project!
The engineers therefore decided to draft a specification for a way to automate and simplify this task. This is how we heard about the project management tool that VINCI Energies makes available under its framework agreement with Microsoft: MSP Online.
How does it work?
Project Online is a collaborative platform made available to us by VINCI Energies Information System (VESI) – that offers extended collaboration, sharing and reporting functions.
It is made up of MS Project (the well-known scheduling tool) and a Web interface, Project Web App, which supports collaboration and access to project data for each user according to his or her access rights.
This tool enables us to better schedule and track our projects, resources and budgets. There are multiple functions:
♦ scheduling: design and reference schedule (for Design Managers);
♦ production tracking: on-line entry of work completed (in hours) for each deliverable (for technicians and DMs);
♦ validation tracking: on-line entry of validation status of deliverables, by the customer (for DMs);
♦ reporting: automatic generation of customised dashboards, notably automatic monthly tally sheets, workload, Online report to be presented at monthly Project Reviews, etc.
In practical terms, we first create a schedule in MS Project to assign workloads to each technician and engineer.
After the project is published, the tasks are automatically displayed in an individual timesheets for each technician and engineer, who fills it out at the end of each workday (i.e., number of hours spent on completing their tasks) and the engineers are thus able to track and validate each deliverable.
Result: we obtain daily (rather than monthly, as before) indicators that are calculated and adjusted automatically. This provides greater transparency, more collaboration and above all a way to adjust action plans more easily according to the consolidated results.
What are the benefits of using MSP Online?
♦ Fewer routine low value-added tasks;
♦ Task automation, thus rapid execution;
♦ More time spent on high value-added tasks such as:
- Analysis and anticipation of action plans
- Control of standards & regulations
- Control of basic job (optimisation)
- Coordination of estimates
- Better team supervision
Thanks to this mass of information, we are able to define a much more precise number of hours per deliverable. By analysing and anticipating work, we can shorten delivery times.
In addition, MSP Online makes it possible to improve team management, by better supporting our technicians in their day-to-day work. For example, those who perform best can receive a bonus for meeting objectives, and for those who do not, the system gives us an opportunity to work together to find solutions. The annual performance review (EIM) can even use the tool, which we did in 2018.
Are you planning further applications?
For the time being, we are only using it in the design phase of all our projects. Later on, we are considering using it on the worksites to support better organisation of the hours and shifts of our on-site teams.
It is still a bit early to look at feedback, but by the end of 2019 we will be in a position to present concrete results.
To obtain more information about MSP Online and the training on offer within the Group, contact :
Mme Najat SAOUF (najat.saouf@cegelec.com)
Tel: 00212.661 89 12 58
To find out more, click here to read the associated document.
Did you like the article ?