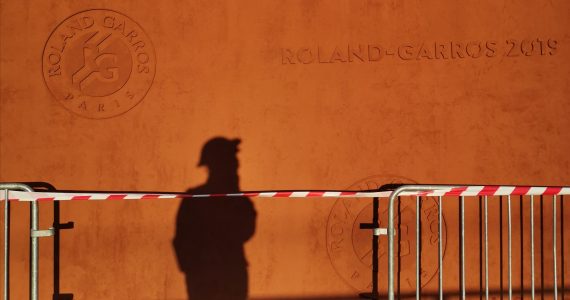
ROLAND-GARROS: A flagship project on a constrained site
The Île de France Service Sector pole has its own project management team, and the scale and complexity of the project has to justify this. That is certainly the case with Roland-Garros, on the edge of the Bois de Boulogne. Antoine GRAND-DUFAY, VEF Tertiaire IDF project director, was previously involved in the construction of the Allianz Riviera in Nice (2011-2013) and the Paris La Défense Arena (2014-2017). Here, he tells us more about this highly unusual project.
What is the role of the project managers?
Project managers ensure control of all coordinated testing for all business units. They also ensure coordination of BIM pre-synthesis studies. We are also the authorised representative of the VE consortium, and manage all contractual aspects of the project day to day.
For Roland-Garros, we are involved as a VCF subcontractor. We effectively mobilised when the contract was signed in 2015 and actively started studies in 2017.
More specifically, I’m responsible for managing the VINCI Energies consortium made up of SAGA Tertiaire for plumbing, Phibor Espaces for high voltage equipment and VDI, and Tunzini Process for HVAC.
What was the FFT (French Tennis Federation) design brief?
In 2015, the FFT put out a call for tenders to modernise and enlarge the Roland Garros Stadium, and cover the Philippe Chatrier centre court with a retractable roof.
This was the first Grand Slam tournament to start this kind of work with major restructuring of the centre court. In a complex situation, VINCI Construction France won the contract ahead of Bouygues.
What is so special about this project?
Roland-Garros is a complex project. We have to complete our works while making sure the competition goes ahead every year.
The big difficulty with this project lies in the combination of major restructuring work in preserved areas, in parallel with new building work.
Only 10% of areas had to be preserved and were eventually largely renovated: players’ reception and changing rooms, players’ bar and restaurant, medical zone, FFT offices and VIP lounges, technical premises.
The centre court is at the heart of this project. Can you tell us more?
So that the tournament would no longer be dependent on the weather, the FFT wanted the centre court covered with a retractable roof.
Covering centre court resulted in the complete renovation of the stadium, because it required rebuilding the entire structure from the foundations up.
This is a mobile covering weighing 3,700 tonnes, or half as much as the Eiffel Tower, incorporating 11 350-tonne rolling gantries, 3 metres high with a span of 105 metres. Only the master girders are actually fixed. The roof will be operational for the 2020 tournament.
Did you use BIM?
Starting from the second floor, the structure is made from a mix of reinforced concrete and metal framework. Traditionally, the framework designer works in 3D. Given the complexity of the facilities being built under the stands, we decided to invest in BIM to make the studies more reliable. The FFT might be interested in making use of this model in the future.
What were the main difficulties? Did you implement specific measures for this project?
Waterproofing was ensured the day before the tournament by applying a resin to the stands: in bad weather, we had water coming into our facilities, which further complicated installation of our electrical boards and water-sensitive equipment.
There were important challenges in terms of safety. We had to carry on our work while thinking about ways to protect structures and people. We immediately started working with VCF, along with the business unit QSE teams and the divisional safety coordinator, Laurence ORDRONNEAU-TEILLET , on the safe deployment of our teams in the presence of water.
Safety was even more important than on other work sites, in terms of support and raising awareness. In the end, almost 250 people were involved during the peak activity period between January and March, with numerous concurrent working issues.
Ultimately, logistics are crucial on a constrained site. There was only one delivery point for major works and other trades. This resulted in a lot of waiting and uncertainty for our deliveries. Most projects now invest in separating these flows. Also, on-site storage was extremely limited. To ease this, we set up rear support bases for each business unit, with dedicated storage areas.
How are things progressing now? What are the next steps?
We will complete 80% of our works in 2019 and the rest in 2020. This year, we’ll be making certain areas available (technical premises, media areas and also player dressing rooms, except for VIP areas).
We’re working hard so the FFT can get the competition ready. After two weeks of status monitoring, we’ll move out to let the FFT dress the site for the event. During the tournament, we ensure maintenance of the installations with cover seven days a week. Then we’ll be back on site the day after the final.
Key figures:
Did you like the article ?